The injection process executed with Polyurethane is performed by sophisticated, revolving machines, normally called "giostre", where different moulds and shapes are applied by article and fit, depending on the orders to be produced.
The materials needed to manufacture the bottom-units is Polyurethane, resulting from the chemical reaction between two liquid compounds, Polyol and Isocyanate, which, mixed up in the same mould, revert from liquid to solid state, perfectly meeting the desired design.
The shape is put on the mould with the upper already inserted, so that the bottom construction tight to the same upper, without using glues or other production-line materials. This particular production method allow to get perfectly sticking, light, flexible and durable bottom-units, with great shock-absorber perfomance levels.
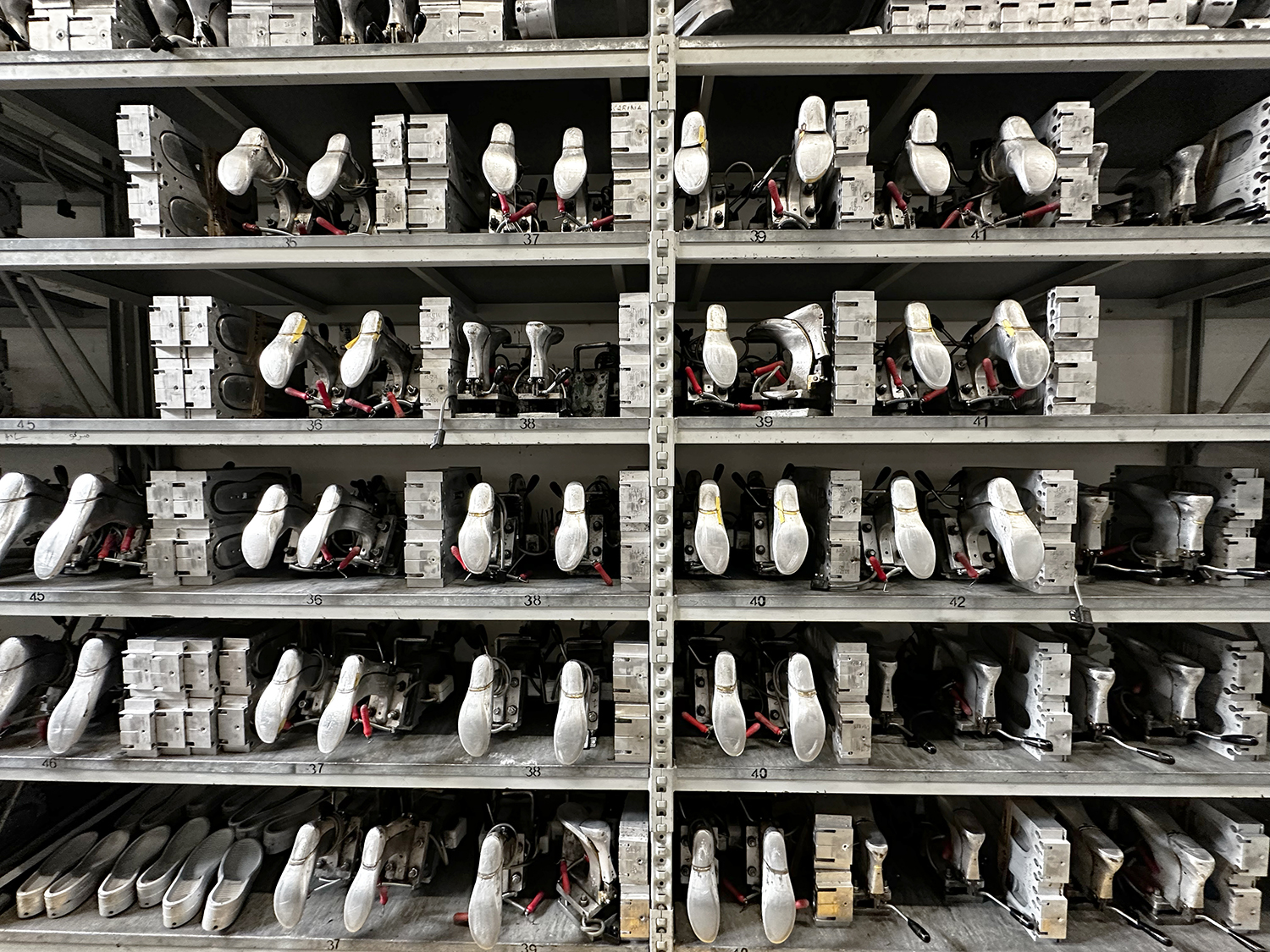
The shoes with polyurethane bottoms offer different benefits and are the best choice for people looking for comfort, durability, good performances.
Lightness
Polyurethane bottom-units make shoes much more comfortable to put on for a long time
Flexibility
These bottom-units are flexible and allow feet natural movements while going for a walk
Shock-absorber
Polyurethane injected shoes offer good shock-resistance performance levels. By absorbing shocks during the walk they reduce feet and joint stress
Wear and tear-resistance
Polyurethane is a wear and tear-resistant material and ensure a greater shoe long-lasting time
Water-resistance
Polyurethane can be treated to make it water-resistant and protect feet from humidity and bad weather